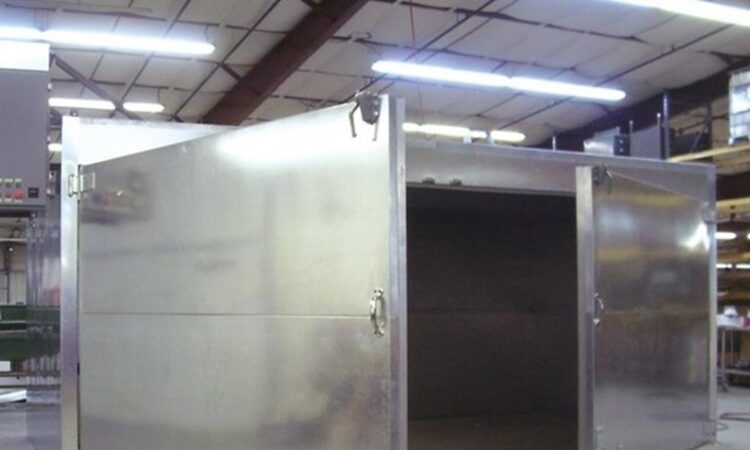
A well-functioning industrial powder coating oven keeps production moving and ensures high-quality finishes, but small oversights can lead to unexpected shutdowns. Preventive maintenance, proper handling, and real-time monitoring can make all the difference in keeping operations smooth. Understanding how to keep an oven running safely while avoiding costly downtime is key for any facility.
Routine Component Checks That Stop Small Issues from Becoming Costly Repairs
Ignoring minor wear and tear on an industrial powder coating oven often leads to bigger failures that halt production. Regular component checks prevent small problems from escalating into major repairs that could take the oven offline for days. Inspections should focus on essential parts such as door seals, insulation, heating elements, and fan motors. Even a small leak in a door seal can disrupt airflow, affecting both efficiency and coating quality.
Operators should create a checklist to track component wear and schedule maintenance before failure occurs. Checking electrical connections for corrosion or loose wires can prevent unexpected power failures. Monitoring belts, bearings, and moving parts reduces friction-related wear, keeping the oven running at peak efficiency. Investing time in these routine inspections saves on costly emergency repairs and keeps production lines moving without interruption.
Keeping Burner Systems Clean to Maintain Optimal Fuel Efficiency
Burners are the heart of an industrial powder coating oven, and when they get clogged with debris or residue, fuel efficiency drops. A poorly maintained burner system can cause uneven heating, wasted fuel, and increased operating costs. Dirty burners also put extra strain on the system, leading to unexpected breakdowns.
To maintain efficiency, operators should clean burners regularly and ensure fuel nozzles are free of obstructions. Checking flame patterns and adjusting air-to-fuel ratios prevents incomplete combustion, which can create temperature inconsistencies. A well-maintained burner not only extends the lifespan of the oven but also ensures an even cure, reducing rework and wasted product.
Real-Time Diagnostics That Catch Performance Fluctuations Before They Cause Downtime
Performance issues don’t always show obvious signs right away, but small fluctuations in temperature, airflow, or fuel consumption can indicate developing problems. Modern industrial powder coating ovens are equipped with diagnostic systems that track these variables in real time, helping operators detect issues before they lead to downtime.
By regularly reviewing diagnostic reports, operators can spot irregularities such as inconsistent heat distribution or slower warm-up times. A sudden drop in airflow might indicate a clogged filter or a failing fan motor, while fluctuating fuel consumption could point to burner inefficiencies. Taking action based on real-time data prevents minor issues from escalating into full system failures, ensuring uninterrupted production.
Proper Loading Techniques to Ensure Consistent Airflow and Maximum Throughput
How parts are loaded into an industrial powder coating oven significantly impacts both curing quality and efficiency. Poor loading techniques can block airflow, leading to uneven heating and inconsistent finishes. Overloading the oven forces the system to work harder, increasing energy use and wear on components.
Operators should follow recommended spacing guidelines to allow heated air to circulate evenly around all parts. Consistency in loading patterns helps maintain predictable cure times and ensures uniform coatings. Training staff on proper rack positioning and weight distribution prevents overloading and minimizes the risk of damage to both parts and the oven itself.
Exhaust System Maintenance That Prevents Heat Buildup and Safety Hazards
A clogged or malfunctioning exhaust system can cause heat buildup, putting both the oven and facility at risk. The exhaust system plays a critical role in venting fumes and maintaining proper temperature balance within the oven. Blocked vents can lead to overheating, causing damage to internal components and increasing the risk of fire.
Routine checks on exhaust stacks, ductwork, and filters prevent dangerous buildup. Operators should inspect for soot accumulation and ensure dampers are functioning correctly to regulate airflow. Keeping the exhaust system clear not only enhances safety but also improves overall oven efficiency by maintaining proper heat circulation.
Emergency Shutdown Protocols That Protect Equipment Without Delaying Production
Unexpected shutdowns can be costly, but knowing how to safely power down an industrial powder coating oven can prevent further damage. Emergency shutdown protocols should be clearly outlined, ensuring all operators know how to react in case of overheating, power failure, or gas supply issues.
Operators should familiarize themselves with manual override controls, allowing them to cut power or fuel supply instantly if needed. Clear communication during an emergency shutdown minimizes downtime by allowing technicians to quickly diagnose and resolve the issue. Having a well-practiced protocol in place prevents panic, protects equipment, and gets production back on track faster.