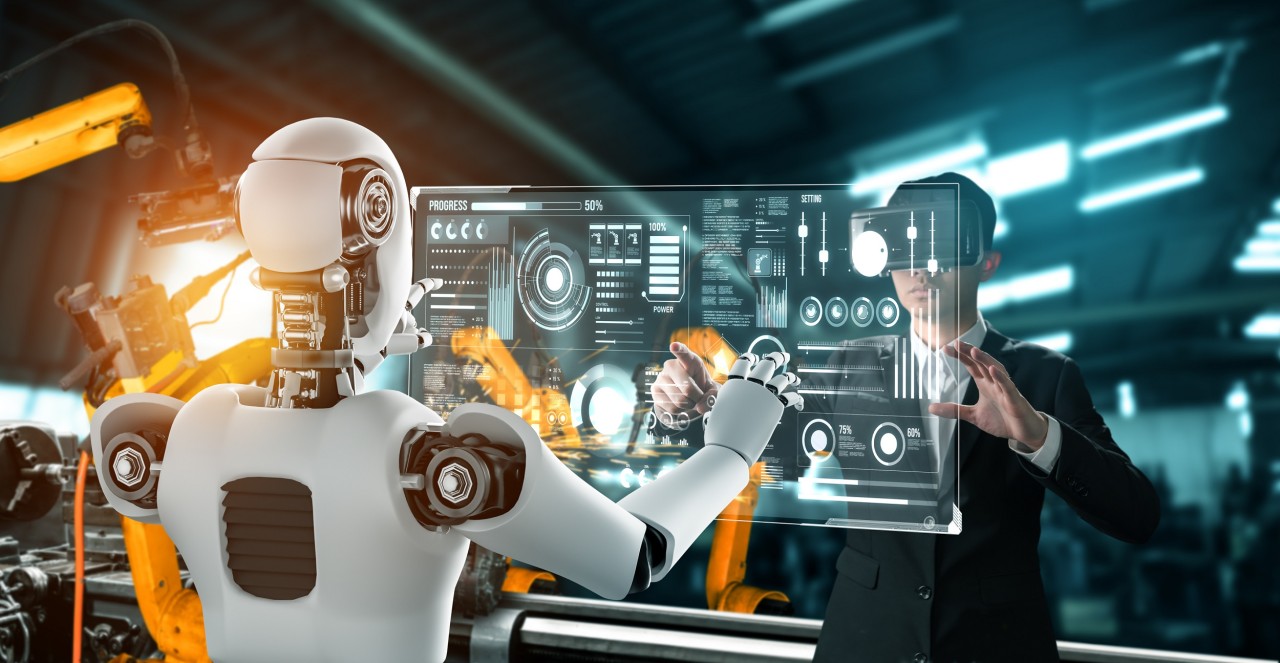
If you’re in the manufacturing business, you know that welding is essential to building strong, durable products. But who says it has to be done solely by human hands? Collaborative welding – a term referring to robots and humans working side-by-side on the same project – revolutionizes how projects are completed.
Not only can this process speed up production times drastically, but it also increases workers’ safety and better customizability of products created. This article will explore how collaborative welding works and why it may benefit your company’s next big project.
Overview of Collaborative Welding and Its Growing Popularity
Collaborative welding is a revolutionary concept in welding technology, quickly gaining popularity in manufacturing. Unlike traditional welding methods, this cutting-edge technique involves advanced welding robots working with skilled human operators. The welding robot is programmed to work collaboratively with the human welder, providing high precision and consistency in the welding process.
This approach enhances productivity and quality and reduces risk to human welders, leading to a safer and more efficient work environment. With the growing demand for high-quality and cost-effective welding solutions, it’s no wonder why collaborative welding is becoming a go-to choice for many manufacturers.
Benefits of Collaborative Welding for Industrial Businesses
Collaborative welding not only speeds up production times but also significantly increases efficiency. With a welding robot working alongside a human welder, tasks can be completed in less time without compromising quality. It is particularly beneficial for large-scale projects with tight deadlines, enabling manufacturers to meet their targets quickly. Furthermore, the consistency provided by robotic welding ensures uniformity in the final product, reducing the need for rework and enhancing customer satisfaction.
Moreover, collaborative welding also enhances safety in the workplace. Human welders can avoid exposure to hazardous fumes and dangerous working conditions by automating specific tasks. It reduces the risk of accidents and improves overall employee well-being. Additionally, as the welding robot handles most heavy lifting and repetitive tasks, human workers can focus on the project’s more strategic and complex aspects.
Challenges Involved in Implementing Collaborative Welding
While collaborative welding offers many benefits, some challenges are involved in implementing this technique. One of the main concerns is the high cost associated with purchasing and integrating welding robots into existing production lines. However, as technology advances, the cost of these robots is expected to decrease.
Another potential challenge is the need for skilled operators to program and operate the welding robots effectively. It requires proper training and expertise, which may take time and resources to develop. However, these challenges can be overcome with appropriate planning and investment in training programs.
What Kinds of Safety Measures Should be Taken to Ensure a Safe Working Environment
Implementing collaborative welding requires careful consideration of safety measures to ensure a safe working environment for humans and robots. Firstly, manufacturers should conduct a thorough risk assessment to identify potential hazards and take necessary precautions to mitigate them. It includes providing human workers with proper personal protective equipment (PPE) and implementing safety protocols when working with welding robots.
Maintaining the welding robots and their surrounding areas is crucial to prevent malfunctions or hazards. It includes periodic inspections, cleaning, and repairing of equipment as needed. Moreover, manufacturers should consider implementing safety features such as sensors and emergency stop buttons on the welding robots for additional protection.
How the Quality and Efficiency of Welded Products are Improved with Collaborative Welding
Collaborative welding improves the quality and efficiency of welded products in various ways. Robotic welding ensures consistency and precision in the welding process, leading to uniformity in the final product. It results in higher-quality finished products with minimal defects.
Moreover, with increased efficiency through faster production times, manufacturers can meet deadlines and take on more projects without sacrificing quality. It can lead to increased revenue and growth for the company. Additionally, robotic welding reduces the need for rework, leading to cost savings in the long run.
The Future of Collaborative Welding in Industrial Businesses
As technology advances, collaborative welding is expected to become even more prevalent in manufacturing. With artificial intelligence and robotics advancements, welding robots will become more sophisticated, versatile, and cost-effective. It will make it easier for smaller businesses to adopt this technique and reap its benefits.
Moreover, as safety standards remain a top priority in the workplace, collaborative welding will become the preferred choice for manufacturers looking to improve worker safety and well-being. It will lead to a more collaborative and harmonious relationship between humans and robots in the welding process.
In conclusion, collaborative welding offers numerous benefits for industrial businesses, including increased productivity, improved quality, and a safer work environment. While there may be challenges in implementing this technique, with proper planning and investment, the rewards far outweigh the risks. As technology advances, collaborative welding will become an essential tool for manufacturers looking to stay competitive.